Destylatory laboratoryjne to urządzenia wykorzystywane w różnych dziedzinach nauki, takich jak chemia, biotechnologia czy farmacja. Istnieje wiele rodzajów destylatorów, które różnią się budową oraz przeznaczeniem. Najpopularniejsze z nich to destylatory prostokątne, kolumnowe oraz rotacyjne. Destylatory prostokątne są najczęściej stosowane do separacji cieczy o różnych temperaturach wrzenia. W przypadku destylacji kolumnowej, proces ten jest bardziej skomplikowany, ale pozwala na uzyskanie wyższej czystości produktów końcowych. Rotacyjne destylatory z kolei charakteryzują się możliwością pracy w niskich temperaturach, co jest istotne przy destylacji substancji wrażliwych na wysoką temperaturę. Wybór odpowiedniego rodzaju destylatora zależy od specyfiki przeprowadzanych badań oraz wymagań dotyczących czystości otrzymywanych substancji.
Jak działają destylatory laboratoryjne i jakie mają zasady działania
Destylatory laboratoryjne działają na zasadzie różnicy temperatur wrzenia substancji, co pozwala na ich separację. Proces destylacji polega na podgrzewaniu cieczy do momentu, gdy zaczyna ona parować. Para następnie przemieszcza się do chłodnicy, gdzie ulega skropleniu i powraca do postaci cieczy. Kluczowym elementem tego procesu jest odpowiednia konstrukcja aparatury, która zapewnia efektywne oddzielanie składników. W przypadku destylacji prostej, proces ten jest stosunkowo szybki i łatwy do przeprowadzenia, jednak nie zawsze wystarcza do uzyskania wysokiej czystości produktu. Dlatego w laboratoriach często stosuje się bardziej zaawansowane techniki, takie jak destylacja frakcyjna czy rektyfikacja. W tych metodach wykorzystuje się kolumny destylacyjne, które zwiększają powierzchnię kontaktu między parą a cieczą, co pozwala na lepszą separację składników o zbliżonych temperaturach wrzenia.
Jakie są kluczowe elementy konstrukcyjne destylatorów laboratoryjnych
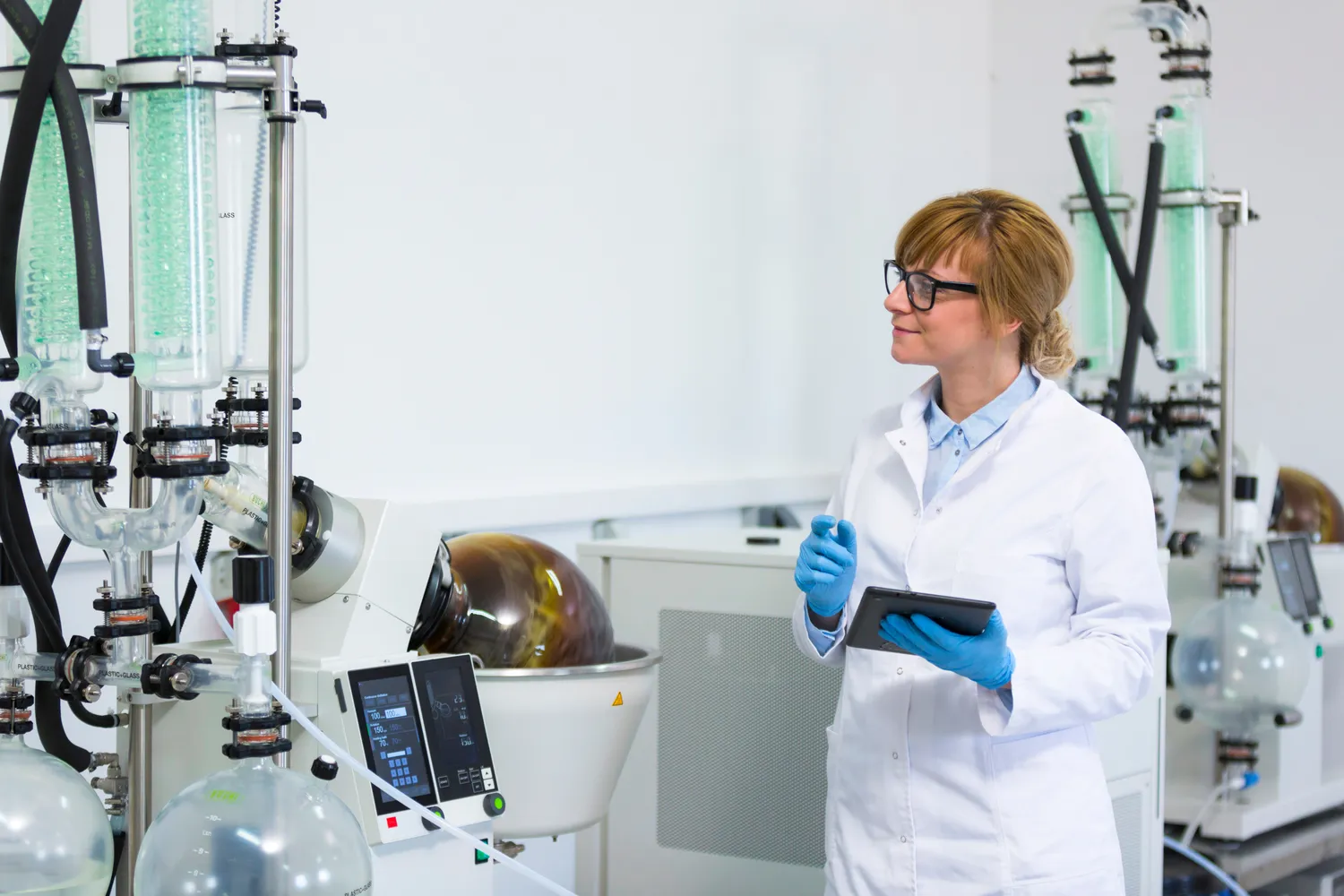
Każdy destylator laboratoryjny składa się z kilku kluczowych elementów konstrukcyjnych, które mają istotny wpływ na jego funkcjonalność oraz efektywność pracy. Podstawowymi komponentami są zbiornik na ciecz źródłową, nagrzewnica, chłodnica oraz zbiornik na produkt końcowy. Zbiornik na ciecz źródłową jest miejscem, gdzie umieszczana jest substancja do destylacji. Nagrzewnica odpowiada za podgrzewanie cieczy do odpowiedniej temperatury wrzenia, co powoduje jej parowanie. Chłodnica natomiast ma za zadanie schładzanie pary i kondensowanie jej z powrotem do postaci cieczy. W bardziej zaawansowanych modelach można spotkać dodatkowe elementy, takie jak kolumny frakcyjne czy różnego rodzaju zawory regulacyjne. Kolumny frakcyjne zwiększają powierzchnię kontaktu między parą a cieczą, co pozwala na lepsze oddzielanie składników o podobnych temperaturach wrzenia.
Jakie są najważniejsze zalety korzystania z destylatorów laboratoryjnych
Korzystanie z destylatorów laboratoryjnych niesie ze sobą wiele korzyści zarówno w kontekście badań naukowych, jak i przemysłowych procesów produkcyjnych. Jedną z najważniejszych zalet jest możliwość uzyskania wysokiej czystości substancji poprzez skuteczną separację składników o różnych temperaturach wrzenia. Dzięki temu można otrzymać czyste związki chemiczne niezbędne do dalszych badań lub produkcji farmaceutyków. Destylatory laboratoryjne są również niezwykle wszechstronne – mogą być wykorzystywane do różnych typów substancji, zarówno ciekłych jak i gazowych. Kolejną istotną zaletą jest możliwość automatyzacji procesu destylacji, co zwiększa efektywność pracy laboratorium oraz minimalizuje ryzyko błędów ludzkich podczas przeprowadzania eksperymentów. Dodatkowo nowoczesne modele destylatorów wyposażone są w systemy monitorujące parametry pracy urządzenia, co pozwala na bieżąco kontrolować przebieg procesu i dostosowywać go do zmieniających się warunków.
Jakie są najczęstsze błędy przy używaniu destylatorów laboratoryjnych
Używanie destylatorów laboratoryjnych, mimo że jest procesem stosunkowo prostym, może wiązać się z wieloma pułapkami i błędami, które mogą wpłynąć na jakość uzyskiwanych produktów. Jednym z najczęstszych błędów jest niewłaściwe ustawienie temperatury nagrzewania. Zbyt wysoka temperatura może prowadzić do degradacji wrażliwych substancji, podczas gdy zbyt niska może skutkować niepełną destylacją. Kolejnym problemem jest niewłaściwe dobranie rodzaju destylatora do konkretnego procesu. Na przykład, stosowanie destylatora prostego do separacji składników o zbliżonych temperaturach wrzenia może okazać się mało efektywne. Ważne jest również, aby regularnie kontrolować stan techniczny urządzenia, ponieważ zanieczyszczenia lub uszkodzenia elementów konstrukcyjnych mogą znacząco wpłynąć na efektywność procesu. Inny częsty błąd to brak odpowiedniej wentylacji w laboratorium, co może prowadzić do gromadzenia się oparów i zwiększać ryzyko pożaru lub wybuchu. Oprócz tego, nieprzestrzeganie zasad bezpieczeństwa, takich jak noszenie odpowiednich środków ochrony osobistej czy korzystanie z urządzeń w odpowiednich warunkach, może prowadzić do poważnych wypadków.
Jakie są nowoczesne technologie w dziedzinie destylacji laboratoryjnej
Nowoczesne technologie w dziedzinie destylacji laboratoryjnej stale się rozwijają, co pozwala na coraz bardziej efektywne i precyzyjne przeprowadzanie procesów separacji. W ostatnich latach pojawiły się innowacyjne rozwiązania, takie jak destylacja membranowa czy wykorzystanie technologii mikrofalowej. Destylacja membranowa polega na wykorzystaniu specjalnych membran, które selektywnie przepuszczają określone składniki mieszanki, co pozwala na ich oddzielanie bez potrzeby podgrzewania. Ta metoda jest szczególnie cenna w przypadku substancji wrażliwych na wysoką temperaturę. Z kolei technologia mikrofalowa umożliwia szybkie podgrzewanie cieczy poprzez zastosowanie fal elektromagnetycznych, co znacznie skraca czas procesu destylacji i zwiększa jego efektywność energetyczną. Ponadto nowoczesne destylatory często wyposażane są w zaawansowane systemy monitorujące i automatyzujące procesy, co pozwala na bieżące dostosowywanie parametrów pracy do zmieniających się warunków. Dzięki tym innowacjom laboratoria mogą osiągać lepsze wyniki badawcze oraz produkcyjne, a także minimalizować ryzyko błędów ludzkich i zwiększać bezpieczeństwo pracy.
Jakie są zastosowania destylatorów laboratoryjnych w różnych branżach
Destylatory laboratoryjne znajdują szerokie zastosowanie w wielu branżach przemysłowych oraz naukowych. W przemyśle chemicznym wykorzystywane są do oczyszczania surowców oraz produkcji różnorodnych substancji chemicznych. Dzięki możliwości separacji składników o różnych temperaturach wrzenia, laboratoria chemiczne mogą uzyskiwać czyste związki niezbędne do dalszych badań czy produkcji. W branży farmaceutycznej destylatory odgrywają kluczową rolę w procesie produkcji leków oraz ich składników aktywnych. Oczyszczanie substancji czynnych za pomocą destylacji pozwala na uzyskanie produktów o wysokiej czystości, co jest niezbędne dla zapewnienia bezpieczeństwa pacjentów. Również w biotechnologii destylatory są wykorzystywane do izolacji i oczyszczania biomolekuł, takich jak białka czy kwasy nukleinowe. W laboratoriach zajmujących się analizą jakości żywności i napojów destylatory służą do ekstrakcji aromatów oraz innych składników smakowych. Wreszcie w przemyśle petrochemicznym destylacja jest kluczowym procesem przy produkcji paliw oraz innych produktów naftowych.
Jakie są wymagania dotyczące bezpieczeństwa przy pracy z destylatorami laboratoryjnymi
Praca z destylatorami laboratoryjnymi wiąże się z pewnymi zagrożeniami, dlatego ważne jest przestrzeganie odpowiednich wymagań dotyczących bezpieczeństwa. Przede wszystkim każdy pracownik powinien być odpowiednio przeszkolony w zakresie obsługi urządzeń oraz zasad BHP obowiązujących w laboratorium. Niezbędne jest noszenie odpowiednich środków ochrony osobistej, takich jak okulary ochronne, rękawice czy fartuchy laboratoryjne, które chronią przed kontaktem z niebezpiecznymi substancjami chemicznymi oraz oparami. Ważne jest również zapewnienie odpowiedniej wentylacji pomieszczenia, aby uniknąć gromadzenia się szkodliwych oparów i zmniejszyć ryzyko pożaru lub wybuchu. Regularna kontrola stanu technicznego sprzętu to kolejny kluczowy aspekt bezpieczeństwa – wszelkie uszkodzenia czy zanieczyszczenia mogą prowadzić do awarii lub nieefektywnej pracy urządzenia. Pracownicy powinni także znać procedury postępowania w sytuacjach awaryjnych oraz umieć korzystać z gaśnic i innych środków ochrony przeciwpożarowej.
Jak wybrać odpowiedni model destylatora laboratoryjnego dla swoich potrzeb
Wybór odpowiedniego modelu destylatora laboratoryjnego zależy od wielu czynników związanych z planowanymi zastosowaniami oraz specyfiką przeprowadzanych badań. Przede wszystkim należy określić rodzaj substancji, które będą poddawane destylacji – różne modele mogą być lepiej przystosowane do pracy z cieczami o różnych właściwościach fizykochemicznych. Kolejnym istotnym aspektem jest wydajność urządzenia; jeśli planowane są duże ilości destylacji, warto rozważyć zakup modelu o większej pojemności lub wydajności pracy. Ważnym czynnikiem jest również łatwość obsługi – nowoczesne modele często wyposażone są w intuicyjne panele sterujące oraz systemy automatyzujące procesy, co ułatwia pracę personelu laboratoryjnego. Dodatkowo warto zwrócić uwagę na materiały użyte do produkcji urządzenia; modele wykonane ze stali nierdzewnej czy szkła borokrzemowego charakteryzują się większą odpornością na działanie agresywnych substancji chemicznych oraz wysokich temperatur.
Jakie są przyszłościowe kierunki rozwoju technologii destylacyjnej
Przyszłość technologii destylacyjnej zapowiada się obiecująco dzięki ciągłemu rozwojowi innowacyjnych rozwiązań i metod pracy. Jednym z głównych kierunków rozwoju będzie dalsza automatyzacja procesów związanych z destylacją, co pozwoli na zwiększenie efektywności pracy laboratoriów oraz minimalizację błędów ludzkich. Systemy monitorujące parametry pracy urządzeń będą coraz bardziej zaawansowane i zdolne do samodzielnego dostosowywania warunków pracy do zmieniających się potrzeb użytkowników. Również rozwój technologii materiałowych wpłynie na konstrukcję nowych modeli destylatorów; materiały kompozytowe czy nanomateriały mogą znacząco poprawić właściwości mechaniczne i chemiczne urządzeń.